What is Produce Transition?
Twice a year, Western produce growers throughout the industry pack up and move equipment, people, and operations 600 miles to be in growing regions where conditions are ideal for the fresh produce that we all enjoy. Certain items need specific temperature ranges and environment to grow to ensure a year-round supply of our favorite produce items. The move itself covers 4 days of round-the-clock work, but planning begins weeks prior as we finalize the last plantings for the region.
Facts / Numbers:
• 2 Transitions each year!
• The majority of the produce industry transitions (Western Growers)
• Truckloads of equipment and materials are loaded
• 600 miles travelled
• It takes about 80 hours from last box to first box
• Long shifts round the clock
Why Transition?
It seems like a lot of work and expense to make such a transition, but the benefits far outweigh the cost and work involved!
• Transition allows continuous supply of produce throughout the year by growing in optimal areas for our produce
• An empty plant allows for detailed maintenance (floors, drains, walls)
• An empty plant allows for deep cleaning and sanitation (above overhead lights, fan coils, shipping racks, etc.)
• There is always a second facility for supply continuity in emergency
This keeps growers near the best growing regions so that:
• Product goes from field to plant quicker
• Less miles traveled equals smaller carbon footprint
• Product is cooled, cut washed, packed, and shipped quicker
Planning
Planning begins for a grower’s projected transition date when they begin planting the last crop for the season. Growers need to balance planning with flexibility to weather and outcome of crop, so the final date could be one week before or after the initial projection of their transition date.
Facility:
• Plant sanitation
• Repairs
• Install New Equipment
• Replaces hoses, tubing, etc.
• Touch ups
Staff:
• Interviews for field / plant workers
• Pre-Season Orientation
• Team Planning for Star in New Region
Product:
• Extra inventory is built up to keep supply continuous during the move
4 Days to Move
Day 1 (Tear Down, Load on Trucks)
• Last production run of product
• Sanitation
• Tear Down of Equipment
-Mechanics, technicians, electricians, supervisors, managers, heavy labor
• Equipment is staged to be loaded on the trucks
• More Sanitation (feet of equipment is scrubbed with a chlorinated alkaline soap)
• Equipment is loaded in order of how they will be reinstalled
• Equipment is spread out the fleet so that production continues even if one truck has an issue
• Chemical pumps and critical equipment are separated on their own truck
• GPS tracking on all trucks to understand arrival times and any delays
Day 2 (Travel Time)
• Equipment is on the road
• Key Team Members fly to the new region
• Rest before Set Up
• Put everything Together
Day 3 (testing)
• Everything is installed
• Testing Begins
• Test Product runs through each line to test every
-Belt
-Dryer
-Scale
-Bagger
• Trouble shooting
• Hand plant over to sanitation teams
Day 4 (Begin Operations)
• Sanitation is finalized
• QA team takes approx. 300 swabs of every food contact surfaces for Listeria
-Drains
-Walls
-Floors
-Equipment legs
• Places with ambient temperatures like Restrooms, breakrooms, truck driver entrances, HR entrances are tested for Salmonella and Listeria
• Machines are getting ready to run
• New and Returning Team onboarding
• Get back to normal production
Communication to Customers
All produce providers transition around the same time, so our customers know the general time frame for transition. When dates are finalized, our customers will hear from the team member handling their account.
This is what you should expect in communications from the people where you buy retail and foodservice produce.
• Ordering dates
• Last day of production in the closing region’s facility
• First day of production in the starting region’s facility
• Status and impact of crops / weather on orders during transition
• Point of contact for any questions or supply challenges
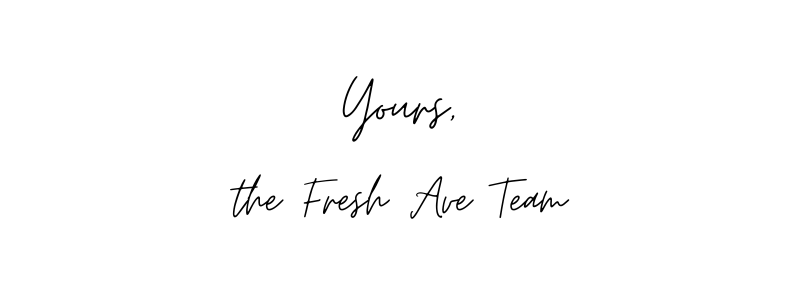